Home » Plastic Manufacturing
Category Archives: Plastic Manufacturing
Plastic Mold Types and Their Applications
Plastic molding is a process that uses heat and pressure to shape polymer. It is a popular method for producing a wide range of products. It can also be used for producing metal parts. Read on American Plastic Molds for more information.
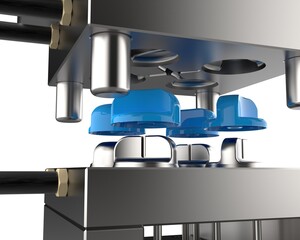
Family molds are ideal for smaller runs, as they reduce the number of injection cycles required. This can help to improve production rates and lower costs.
Injection moulding is a great plastic manufacturing technique that can handle high-volume production runs. The process uses a custom-designed mold that resembles the product part you need, which is then split into two halves and clamped together using hydraulic rams. The injection machine then injects the raw polymer into the mold’s cavities and a screw pushes it through. This increases the temperature of the raw material, allowing for better flow, and reduces Van der Waals forces between molecules that can hinder movement in a low-temperature state. This creates a homogenous blend that is easier to shape and gives the finished part its desired finish.
This process can be used to produce a wide range of polymers, including all thermoplastics and some thermosetting plastics. This versatility makes this type of injection molding well-suited for a number of different industries and applications. However, each polymer has its own unique set of requirements when it comes to injection moulding. A good injection moulding manufacturer will have extensive knowledge of how each type of plastic behaves in this process and how best to manipulate it for a specific end result.
The design process for plastic parts produced with this method begins with a detailed 3D model created in CAD software. These models serve as the blueprint for the molded part, with consideration given to factors such as large undercuts (to allow the part to be easily ejected from the mold) and proper draft angles and wall thickness to ensure that the resulting part will be strong and durable.
Another important factor to consider is the injection moulding machine itself. A reliable machine will operate swiftly, boosting production rates and helping to lower costs per unit. It should also be user-friendly with easy-to-use controls and software that can adapt to changing production needs without additional retooling.
One of the most significant benefits of injection moulding is its ability to produce parts with an exceptional finish that is both aesthetically pleasing and durable. This can reduce or even eliminate the need for further post-production processing like painting or polishing, saving time and money. Additionally, this type of plastic manufacturing is able to achieve a very high level of strength by adding fillers into the molten plastic. This helps to add weight and density to the final product, making it a more robust and longer-lasting alternative to other plastic manufacturing processes.
Extrusion Moulding
This is a common manufacturing process for making different types of plastic products. It involves forcing molten plastic through a 2d die to form it into a specific shape. This is a popular choice for manufacturing things like curtain tracks, straws, rods, and wire insulation. It is also good for making products that need a large number of lengths of the same essential design/product. It has the advantage of being more cost-effective than injection molding, since it can produce multiple parts at one time. It can also be used to create products that need internal features without the need for a draft, and it generally produces a smooth surface finish.
It is ideal for making hollow pipes and tubing, such as PVC water and sewer pipes, as well as many other industrial, commercial and medical applications. It is also good for making plastic films, thin sheeting and coatings, wire insulation, filaments, and fibres. Drinking straws, motor fuel lines, window glazing and glass replacements, and ‘blister’ packaging are other examples of this type of product.
One major benefit of extrusion moulding is that it produces less waste than injection molding. This is because any trimmed material from the end of a run can be ground up and fed back into the machine, to be reintroduced into the manufacturing process. This is a great way to reduce material costs and ensure that all of the plastic used in production gets put to good use.
While the advantages of extrusion moulding are considerable, it is important to consider the environmental impact of this method of production before making a decision. The production of plastic products, including extruded plastic, requires a significant amount of fossil fuels. This contributes to climate change and greenhouse gas emissions, and it can take hundreds of years for some plastics to break down in the environment.
As with injection molding, it is possible to add fillers to the melted plastic to enhance its strength and resilience. However, this is usually only done when producing a high volume of the same product. It is not as suitable for small batches, because it is expensive to build the molds for each new product.
Rotomoulding
Unlike injection moulding, which requires pressure to force the plastic into the mold, rotomoulding relies on gravity and centrifugal forces to spread the molten material around the cavity. This allows the operator to achieve greater levels of control over wall thickness, which is crucial to a product’s strength and durability. The rotational process also helps prevent the formation of air bubbles within the resulting hollow plastic product.
When the plastic is cooled, the product’s walls are solidified and become rigid. The rotomoulding process also produces stress-free products, meaning they are less likely to deform or crack during use. This is achieved through the rotational process and a careful selection of the type of plastic used. Polyethylene (PE) is a popular choice for rotational molding, due to its low cost and high heat resistance. It can be found in a wide range of sizes, from toys to 50,000-litre tanks.
The rotary process also enables the production of complex shapes, including curves and angles. This makes it ideal for producing tanks and leisure craft, but also medical equipment, children’s toys, and more. However, the limiting factors for this type of plastic moulding are the need for additional equipment to speed up the cooling process and the inability to automate the process.
One of the biggest benefits of rotomoulding is that it uses a very low amount of raw materials, making it more sustainable than other methods of producing hollow plastic products. Furthermore, rotomolded plastics are often made from recycled materials, which reduces the need to mine fresh materials and helps to minimize environmental impact.
Another benefit of this method is that it allows for the manufacturing of large plastic products, such as TranPak’s MegaBin. This plastic hopper bin is a perfect example of how the combination of the right plastic and rotational moulding can produce a high-quality, robust product that is suitable for an array of applications. To find out more about how rotomoulding can benefit your business, contact us today. Our team of experts can advise on the most appropriate plastic for your application and recommend the best manufacturing technique to suit your needs.
Cast Moulding
Cast molding is used to produce a wide range of products, from small automotive components to kitchenware. It involves pouring liquid plastic into a mold and then allowing it to cure. This process allows for tight tolerances, meaning that the final product will be very accurate in terms of shape and size. It also offers flexibility, as the mold can be altered to accommodate changes in design.
One of the main benefits of using this type of mold is that it is relatively inexpensive and quick. Unlike injection molding, which requires a large upfront investment in tooling, urethane casting can be done for under $2,000, making it the ideal option for entrepreneurs looking to keep costs low.
Another benefit of this method is that it produces high-quality products. The liquid plastic poured into the mold is heated, which helps to create a smooth, dense surface. This helps to prevent warping, dents, and other defects that can occur in the final product.
This method of molding is also very versatile, as it can be used to create any type of object. In addition, it can be used to make prototypes, allowing entrepreneurs to test their ideas before investing in expensive production-quality tools. Additionally, the mold can be made of a variety of materials, including polyurethane and polyester.
A downside of this type of molding is that it can be difficult to remove the finished product from the mold. This can be overcome by using a technique called pressure casting. This involves putting the finished product on a piece of wood and applying pressure to it, allowing the resin to pull away from the object. This can also help to eliminate air bubbles, which can be problematic in some cases.
Despite these challenges, cast moulding is an excellent way to make a wide range of products. It is important to choose the right resin and mold material for your project, though, to ensure that it will be durable and long-lasting. It is also important to know how to properly mix the resin and to use a proper mold to ensure that the product will be as clean and smooth as possible. This will ensure that your final product is of the highest quality possible.